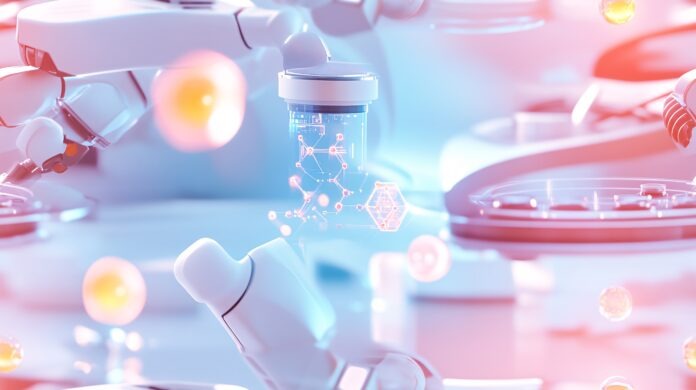
The production of sterile products involves reducing the risk of microbiological, particulate, and endotoxin or pyrogen contamination through advanced technologies, qualified personnel, and effective monitoring systems. The EU GMP Annex 1 guidelines emphasize the importance of a Contamination Control Strategy (CCS) that involves all stages of production and critical areas of the process. The goal is a holistic risk management approach to ensure that all control points are adequate and that the system is prepared to detect and mitigate contaminations.
Principles of sterile product production
Chapter 2 of the EU GMP Annex 1 guidelines reiterates that sterile production must include scientifically based procedures evaluated through Quality Risk Management (QRM) criteria. The recommended approach includes adopting specific technologies, such as isolators, RABS (Restricted Access Barrier Systems), and rapid transfer systems, to minimize human interaction in critical areas. These technological tools, combined with effective CCS management, must work synergistically to prevent contamination risks. End-point testing alone should never be relied upon; quality control must be integrated throughout the production process to ensure regulatory compliance and the safety of the final product.
CCS: a holistic approach to contamination prevention
The contamination control strategy requires assessing all critical points and adopting both technical and organizational control measures. This strategy is not just a regulatory requirement but an operational philosophy that integrates risk assessment with continuous monitoring and process improvement. As highlighted by the guidelines, the effectiveness of this strategy depends on careful facility design, selection of materials and equipment, and a quality management system that is constantly updated according to innovations and production conditions.
Pharmaceutical Quality System (PQS)
The Pharmaceutical Quality System (PQS) must be specifically oriented toward the production of sterile products, with a particular focus on managing associated risks. Chapter 3 of the EU GMP Annex 1 guidelines introduces specific elements for sterile products, emphasizing that the quality system must include control measures for each stage of the production process, including periodic evaluations and quality reviews. A crucial element of the PQS is supporting CCS documentation, which must be kept up to date and reflect process trends concerning contamination risks.
Risk Assessment and Proactive Management
The guidelines require the pharmaceutical quality system to integrate proactive risk management, with documentation allowing for real-time monitoring of the contamination control system. Among the proposed actions, periodic risk and control reviews enable prompt response to process changes, while deviation management and batch reviews complete the PQS framework. Additionally, the PQS must support change management that can promptly incorporate all necessary impact assessments.
Personnel Requirements: training and qualification
One of the most important aspects of sterile product production is personnel training and qualification. According to Chapter 7 of the EU GMP Annex 1 guidelines, personnel working in critical environments must have specific training, adequate skills, and a thorough understanding of the processes and risks related to sterility. Personnel qualification is not a one-time act but requires continuous updates and periodic review, with criteria ensuring that only properly qualified personnel can access sterile production areas.
Guidelines for qualification and conduct
Personnel must follow strict standard operating procedures, including proper attire for sterile areas and adherence to aseptic techniques. The holistic approach of the CCS requires every operator to be aware of the importance of their role in contamination prevention. For this reason, the guidelines recommend training that includes practical simulations and contamination case analysis. Operators must demonstrate competence in handling sterilization tools and applying preventive measures, with particular attention to aseptic interventions and the use of protective equipment.
Performance monitoring and continuity of qualification
Monitoring personnel performance is a key element in maintaining high-quality standards. In this regard, periodic qualification reviews and monitoring of operational performance allow timely identification of potential gaps. The personnel qualification system should also include a review of unscheduled intervention cases and corrective measures in case of deviations from sterility protocols, thus ensuring safe and compliant operational continuity.
Conclusion: an Integrated System for Sterile Product Quality
The adoption of an integrated and documented CCS, a PQS specifically for sterile production, and personnel training are fundamental pillars for a compliant and safe production environment. Quality management in sterile production requires ongoing technology updates, application of risk management principles, and active performance monitoring, enabling the maintenance of the standards required to ensure the safety of pharmaceutical products. The EU GMP Annex 1 guidelines provide a framework that, when properly implemented, allows these objectives to be achieved, confirming the importance of a holistic approach to contamination prevention and final product quality.